Úvod of Label Printing Defects
Label printing defects can pose a significant challenge for manufacturers and businesses that rely on precise and consistent labeling. Among these defects, color consistency stands out as one of the most prevalent issues. Addressing this problem requires a comprehensive understanding of its root causes and a strategic approach to overcome it.
Color Consistency Issues
One of the most common label printing defects is inconsistency in color. This issue can stem from various factors, including the quality of ink, printer calibration, and the type of substrate used. Understanding these elements is crucial to effectively address and correct color consistency problems.
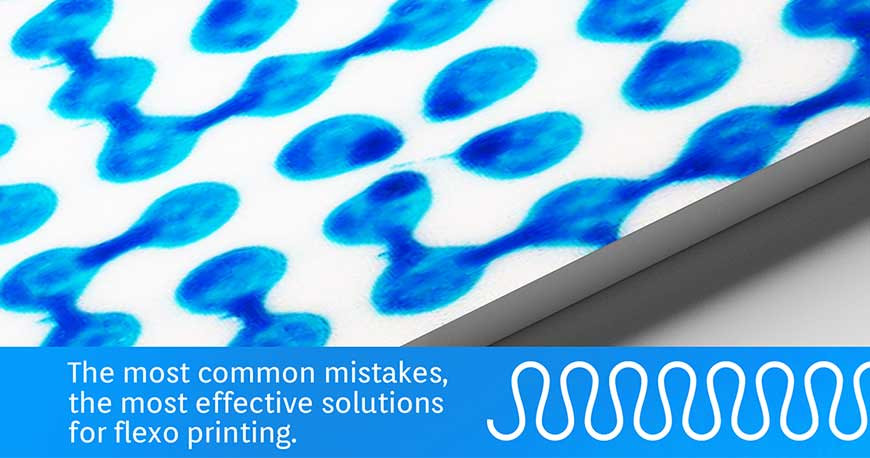
Importance of High-Quality Inks
Choosing the right ink is the first step in preventing color inconsistency. Low-quality inks often lead to poor color reproduction, resulting in label printing defects that appear faded, dull, or uneven. Additionally, using an ink type that doesn’t match the substrate can exacerbate these issues, leading to unsatisfactory label appearance.
Significance of Printer Calibration
Regular printer calibration is essential for maintaining color accuracy. Calibration involves fine-tuning the printer’s settings, such as ink flow rate and print head alignment, to ensure consistent color output. Neglecting this step can result in labels with uneven color distribution, where some areas are noticeably darker or lighter.
Impact of Substrate Selection
The choice of substrate plays a crucial role in color consistency. The substrate’s properties influence how the ink is absorbed and the label’s final appearance. For instance, a substrate that is too porous may cause the ink to spread unevenly, while a dense substrate might make the ink look dull or faded.
Environmental Conditions
Environmental factors like temperature and humidity can also affect the outcome of label printing. Printing in hot or humid conditions can lead to uneven ink absorption, further complicating color consistency. It’s important to control these conditions to ensure optimal printing results.
Steps to Avoid Label Printing Defects
Investing in Quality Materials
To correct color consistency issues, investing in high-quality inks and substrates specifically designed for label printing is crucial. These materials are formulated to work together, reducing the likelihood of defects.
Regular Printer Calibration
Routine calibration of printing equipment ensures that the colors produced are accurate and consistent. This practice helps maintain the quality of the labels and reduces the risk of color inconsistency.
Using a Color Management System
Implementing a color management system can further enhance color consistency. This system ensures that the colors produced by the printer match the intended design, providing a reliable solution for maintaining color accuracy.
Specialized Label Printing Services
For businesses looking to guarantee color consistency, utilizing a label printing service with expertise in this area can be beneficial. These services have the necessary equipment and knowledge to produce high-quality, consistent labels.
Záver Label Printing Defects
Correcting color consistency in label printing is a multifaceted task that involves selecting the right inks and substrates, regularly calibrating printers, and managing environmental conditions. By taking these steps, manufacturers and businesses can achieve high-quality labels that meet their standards for accuracy and consistency.
Summary FAQ on Label Printing Defects
1.What are common label printing defects?
One of the most common label printing defects in label printing is color inconsistency, which can result from issues with ink quality, printer calibration, and substrate selection.
2.How does ink quality affect label printing?
Using low-quality inks can lead to faded, dull, or uneven colors on labels. It’s important to choose inks specifically designed for the type of label printing being done.
3.Why is printer calibration important?
Regular printer calibration ensures that colors are reproduced accurately and consistently. Without proper calibration, labels may have uneven color distribution.
4.How does substrate selection influence color consistency?
The substrate, or material on which the label is printed, affects how ink is absorbed. A substrate that is too porous or too dense can cause color inconsistencies, such as uneven or dull appearances.
5.What environmental factors can impact label printing?
Temperature and humidity can influence how ink is absorbed and can lead to color inconsistencies. Controlling these environmental conditions is key to maintaining consistent label quality.
6.What steps can be taken to correct color consistency in label printing?
To correct color consistency, businesses should invest in high-quality inks and substrates, regularly calibrate printers, consider using a color management system, and potentially use specialized label printing services.
7.What is a color management system, and how does it help?
A color management system ensures that the colors produced by the printer match the intended design, helping maintain color accuracy and consistency throughout the printing process.