Introduction of Silicone Rubber
Silicone rubber is a versatile material widely used in industries ranging from automotive to electronics and healthcare. Its unique properties, such as flexibility, resistance to extreme temperatures, and chemical stability, make it an essential component in various products. Understanding the manufacturing process of silicone rubber not only sheds light on how it achieves these properties but also highlights its significance in modern applications.
In this article, we’ll explore the detailed manufacturing process of silicone rubber, starting with the raw materials, moving through mixing and molding, and ending with the finishing touches. Each step plays a critical role in ensuring that silicone rubber meets the stringent quality standards required for its diverse applications.
Raw Materials Used in Silicone Rubber Manufacturing
Before delving into the manufacturing process, it’s important to understand the key raw materials involved:
Silicone Base
The primary ingredient in silicone rubber is the silicone polymer, a substance derived from silica (sand). Silicone polymers provide the rubber with its core properties, such as flexibility, heat resistance, and durability. The quality of the silicone base directly influences the performance of the final product.
Fillers and Additives
Fillers such as silica or carbon black are often added to improve specific properties, like tensile strength or resistance to abrasion. Additives, on the other hand, can be introduced to enhance features like color, UV resistance, or flame retardancy. The selection of fillers and additives depends on the intended application of the silicone rubber.
Catalysts and Crosslinking Agents
To initiate the curing process, catalysts are used to trigger a chemical reaction, transforming the liquid silicone into a solid, rubbery material. Crosslinking agents help form a three-dimensional network of bonds, giving the rubber its elastic properties.
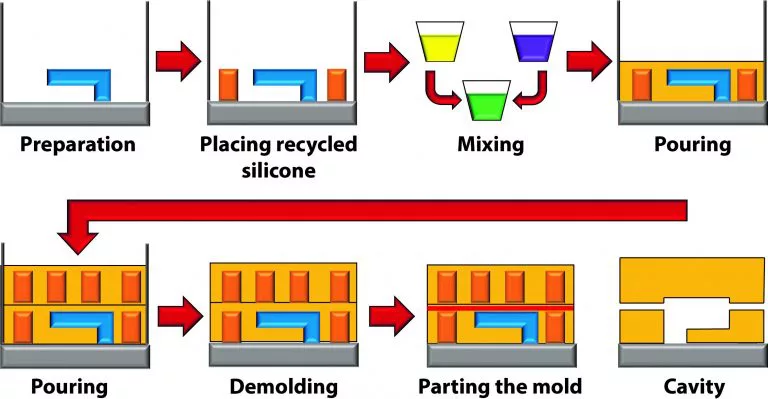
Mixing and Preparation of Raw Materials
Once the raw materials are selected, the next step is to blend them into a homogenous mixture.
Mixing Process
The silicone base, fillers, additives, catalysts, and crosslinking agents are combined in industrial mixers. The aim is to ensure that all components are evenly distributed, which is crucial for the consistency of the final product. Precision in the mixing process helps achieve the desired mechanical and physical properties of the rubber.
Degassing
After mixing, the compound undergoes a degassing process to remove any trapped air bubbles. Air pockets can compromise the strength and uniformity of the silicone rubber, leading to defects in the final product. Vacuum degassing is commonly used to achieve a bubble-free mixture.
Testing the Mixture for Consistency
Before moving to the molding stage, the mixture is tested to ensure it meets specific viscosity and flow properties. Any deviation from the standard could impact the molding process or the performance of the final product, making this a vital quality control step.
Molding and Curing Process
Once the silicone rubber compound is prepared, it’s ready for molding and curing. This stage is where the rubber takes on its final shape and properties.
Injection Molding
Injection molding is one of the most common methods used for manufacturing silicone rubber products. In this process, the liquid silicone is injected into a mold cavity under high pressure. This allows for the creation of complex shapes with precision, making it ideal for producing parts used in the automotive and electronics industries.
Compression Molding
Another technique is compression molding, where the silicone compound is placed in a pre-formed mold cavity and compressed under heat and pressure. This method is suitable for producing large or simple silicone rubber components, such as gaskets or seals.
Vulcanization Process
Vulcanization, also known as curing, is the process that converts the silicone compound into a stable, elastic material. Heat is applied to accelerate the chemical reaction triggered by the catalysts, resulting in the crosslinking of silicone molecules. Depending on the type of silicone, this process can take minutes or hours.
Post-Curing and Finishing
Once the silicone rubber has been molded and cured, it undergoes several finishing steps to ensure quality and usability.
Cleaning and Inspection
The molded parts are first cleaned to remove any residual materials. Afterward, they are thoroughly inspected for any defects such as surface imperfections or inconsistencies in shape. This inspection process ensures that only parts meeting strict quality standards proceed to the next stage.
Testing for Quality Control
Silicone rubber products are subjected to various tests to ensure they meet the required specifications. These tests may include tensile strength, hardness, and resistance to environmental factors like heat or chemicals. Rigorous quality control helps maintain the reliability and performance of silicone rubber products.
Packaging and Distribution
Once the products have passed all quality checks, they are packaged according to their application requirements. The packaging is designed to protect the silicone rubber parts from environmental damage during storage and transportation. Finally, the products are distributed to various industries for use in their respective applications.
Applications of Silicone Rubber in Different Industries
Silicone rubber is highly valued across a wide range of industries due to its versatile properties.
Automotive
In the automotive industry, silicone rubber is used for parts like gaskets, seals, and hoses. Its resistance to extreme temperatures and harsh chemicals makes it ideal for components exposed to the rigors of automotive operation.
Electronics
In electronics, silicone-rubber plays a crucial role in insulating and protecting delicate components. It’s commonly found in keypads, connectors, and seals, where it provides durability and resistance to moisture and electrical conductivity.
Medical
In the medical field, silicone-rubber is prized for its biocompatibility. It’s used to manufacture medical devices such as catheters, implants, and tubing. The material’s flexibility and resistance to sterilization processes make it ideal for these sensitive applications.
Commonly Asked Questions About Silicone Rubber Manufacturing Process
1.What are the different types of silicone rubber?
Silicone rubber comes in various types, including liquid silicone rubber (LSR), high-consistency rubber (HCR), and room-temperature vulcanizing (RTV) silicone. Each type is tailored for specific applications based on its properties, such as flexibility, hardness, or curing temperature.
2.How is silicone rubber different from other types of rubber?
Compared to natural rubber or synthetic rubbers like neoprene, silicone-rubber offers superior resistance to extreme temperatures, chemicals, and UV light. Its biocompatibility also sets it apart, making it suitable for medical applications where other rubbers might not perform as well.
3.What are the key considerations for quality control in silicone rubber manufacturing?
Key factors include ensuring uniformity in the raw material mixture, eliminating air bubbles, controlling curing times, and conducting rigorous testing for physical and mechanical properties. Proper quality control ensures that the final product meets industry standards and performs reliably in its intended application.
Conclusion
The manufacturing process of silicone rubber is a complex yet finely tuned operation that balances the right selection of raw materials, precision in mixing, and careful molding and curing techniques. Post-production steps such as quality control and finishing ensure that silicone rubber products meet the high standards required for industries like automotive, electronics, and medical applications.
From its flexibility to its durability, silicone-rubber continues to be a material of choice for countless applications, and understanding its manufacturing process gives us insight into why it remains indispensable in modern industry.